
PUFFERN, SORTIEREN und KOMMISSIONIEREN
Effizienzsteigerung durch Materialflussoptimierung
Die zunehmende Variantenvielfalt bei gleichzeitiger auftragsbezogener Stückzahl-1-Fertigung macht es notwendig, ein größeres Augenmerk auf die Optimierung der Materialflüsse in der Produktion zu legen, um die Bearbeitungsmaschinen und Materialien noch effizienter nutzen zu können.
Die Optimierung des Materialflusses mithilfe eines Kompaktsortierspeichers kann wesentlich dazu beitragen.
Unter Verwendung eines Kompaktsortierspeichers werden die Werkstücke zwischen den einzelnen Bearbeitungsschritten zwischengepuffert und in einer neuen, optimierten Reihenfolge für den folgenden Bearbeitungsschritt Just-in-time zur Verfügung gestellt. Dies ermöglicht nicht nur die Optimierung des Fertigungsprozess bei der Herstellung von Möbelteilen, sondern eröffnet ganz neue Möglichkeiten für eine rationelle Fertigung.
Die Optimierung des Materialflusses mithilfe eines Kompaktsortierspeichers kann wesentlich dazu beitragen.
Unter Verwendung eines Kompaktsortierspeichers werden die Werkstücke zwischen den einzelnen Bearbeitungsschritten zwischengepuffert und in einer neuen, optimierten Reihenfolge für den folgenden Bearbeitungsschritt Just-in-time zur Verfügung gestellt. Dies ermöglicht nicht nur die Optimierung des Fertigungsprozess bei der Herstellung von Möbelteilen, sondern eröffnet ganz neue Möglichkeiten für eine rationelle Fertigung.
Dieses Video wird bei Aktivierung von Google YouTube nachgeladen.
Es gelten die Datenschutzerklärungen von Google.
Es gelten die Datenschutzerklärungen von Google.
Anwendung
Anwendungsbereiche
Die Anwendungsbereiche ergeben sich aus den unterschiedlichen Fertigungsschritten der jeweiligen Produkte, so beispielsweise in der Möbelfertigung:
Plattenzuschnitt – Kantenbearbeitung – Bohren – CNC Bearbeitung – Oberfläche – Montage – Verpackung.
Aber auch in anderen Branchen stellen sich dieselben Aufgabenstellungen.Ziele eines Kompaktsortierspeichersystems:
- Optimierung der aktiven Bearbeitungszeiten,
- Optimierung der Umrüstzeiten,
- Glättung der Spitzenauslastungen in mehr durchschnittliche Auslastungen,
- gleichmäßigere Produktion, aber immer unter der Prämisse „Losgröße 1“,
- Zulassen von mehreren aktuellen Aufträgen zum nächsten Versandtermin und von künftig folgenden Aufträgen mit gleichen Bearbeitungen – sogenannte „Kann-Teile“ – mit späterer Zuteilung aus dem Puffer,
- gleiche Fertigungszeiten für A-Ware und B- und C-Ware zu erreichen,
- just-in-time aus dem Speicher die Bearbeitungsmaschinen zu füttern,
- bestmögliche Ausnutzung der Ressourcen,
- Minimierung von Abfällen.
Diese verschiedenen Aufgabenstellungen können einzeln, aber auch kombiniert durch den Kompakitsortierspeicher bearbeitet bzw. optimiert werden.
Die Verwaltung der Bestände als auch die Steuerung der gesamten Abläufe sowie die Optimierung anhand der festgelegten Kriterien erfolgt über ein Fertigungsleitsystem.
Einlagerung und automatische Chargenbildung
Die in den Kompaktsortierspeicher einlaufenden Werkstücke werden mittels Barcode identifiziert. Je nach Teilelänge werden entsprechend der Sektionslängen im Sortierspeicher mehrere Teile gesammelt und dann als Lage durch das stehende Bediengerät mittels Teleskopen aufgenommen.
Im Idealfall können alle Teile innerhalb einer Ebene eingelagert und gespeichert werden. Im schlechtesten Fall muss jedes einzelne Teil in eine andere Ebene abgelegt werden - je nach Sortierkriterium.
Für den folgenden Bearbeitungsschritt, wie z.B. an einer Kantenbearbeitungsmaschine, werden im Sortierspeicher automatisch Chargen entsprechend den Prioritäten, wie z.B. Dicke, Farbe, Kantentyp, Kantenfarbe oder Leimfarbe, zusammengestellt.Höhere Auslastung der Bearbeitungsmaschinen
Bei der Chargenbildung wird versucht, die Kantenbearbeitungsmaschine maximal zu belegen und möglichst weniger Umrüstzeiten zu haben. Ziel ist es, eine kontinuierliche Auslastung der Bearbeitungsmaschinen zu erreichen.
Werkstücke, die in nur einem Umlauf fertig gestellt sind, werden aus dem Umlauf ausgeschleust und durch ein nachfolgendes Werkstück wieder ersetzt, so dass keine Leerläufe an den Maschinen entstehen.
Sortierkriterien
Typische Sortierkriterien bei der Möbelteilfertigung:
- Kantenvorschau mit Zieldaten der jeweiligen Zuführung
- Sägenoptimierung mit Resteerfassung und -verwaltung
- Einlauf mit Vorsortierung und Zuteilung, beispielsweise zur Kantenbearbeitung in Dicke, Kantentyp, Kantendekor, Klebstoff und Auftragsnummer oder zur Säge
- Plattendicken
- Kantenfarben
- Klebstofffarben
- Bohrbilddaten
- Auswahl Bohrmaschine/CNC, welche Art der Bearbeitung dauert an welcher Maschine länger?
- Auswahl/ Zuteilung zur Maschine allgemein
Individuelle Festlegung der Sortierkriterien
Die Sortierkriterien werden kundenspezifisch in Abstimmung mit dem Kunden festgelegt und entsprechend in der Software berücksichtigt. So besteht auch die Möglichkeit, unterschiedliche Ziele der Bearbeitung zu deklarieren und mehrere Umläufe für ein und dieselbe Maschine mit jeweils weiteren Umsortierungen im Speicher durchzuführen.
Die Rückkehr der Werkstücke in den Kompaktsortierspeicher kann entsprechend der erforderlichen Bearbeitungsschritte theoretisch beliebig oft wiederholt werden.Berücksichtigung zusätzlicher Parameter
Bevor Teile vom Fertigungsleitsystem angestoßen werden, berücksichtigt die Software die Dicken, Farben und die Ausführung der späteren Kanten sowie den aktuellen Füllstand des Kompaktsortierspeichers. Dabei findet die Vorschau auf alle Folgeprozesse hinter dem Speicher ebenso Berücksichtigung.
Erst nach Erfüllung dieser Parameter fordert die Sägenoptimierung die nächste Platte für den Zuschnitt an. Um bessere Möglichkeiten zur Schnittplanoptimierung zu bekommen, lässt das System zu, Teile späterer Aufträge bereits zuzuschneiden, die dann im Sortierspeicher gepuffert werden. Die dennoch entstandenen Reste werden erfasst und mitverwaltet.
Inhalt des Fertigungsleitsystems
1 . Sortierpuffer inkl. der Transportstrecken zum Zu- und Abführen der Teile
- Bestandsmäßige Verwaltung des Pufferlagers
- Steuerung und Überwachung aller Transportstrecken
- Steuerung der Bediengeräte
- Visualisierung der gesamten Anlage
- Umsetzung der Sortierlogik
- Übersichten über den aktuellen Bestand im Sortierlager und dem Fortschritt der Sortierung
- Möglichkeiten zum manuellen Eingriff, z.B. Sonderauslagerungen von Teilen oder Ändern der Reihenfolge der Lose
- Optimierung der Transportbewegungen, um möglichst viele Teile pro Takt ein- bzw. auszulagern
2. Verplanungsmodul
- Import aller notwendigen Daten vom Kunden
- Speicherung der Daten in einer Datenbank
- Zentrales Verplanungsmodul für den Zuschnitt
- Anzeige aller ausstehenden Aufträge für die Säge
- Gruppierungsmöglichkeiten für die Anzeige und Auswahl der zu fertigenden Teile
- Erzeugung von Fertigungslosen, bezogen auf die Sortierkapazität der Anlage
- Anzeige des Füllstandes des Sortierers
- Datenübergabe an den Optimierungskern
- Übernahme der Optimierungsergebnisse
- Drucken von Bereitstellungslisten für den Zuschnitt
Umsortieren für den folgenden Bearbeitungsschritt
Die Werkstücke, die aus der Kantenbearbeitung zurück in den Speicher kommen, werden unter Beachtung des nächsten Bearbeitungsschrittes, wie z.B. Bohren oder CNC-Bearbeitung, neu sortiert und eingelagert.
Nach der Bildung einer neuen Charge wird diese dann ausgelagert und dem folgenden Bearbeitungsschritt zugeführt, ebenfalls unter der Berücksichtigung der speziellen Anforderungen und Kriterien an das Teil oder an die technischen Möglichkeiten der Maschine.Optimaler Durchlauf von Anfang an
Das ist System ist in der Lage, die erforderlichen Teile z. B. für die nachfolgende Montage oder Verpackung vollautomatisch neu in die richtige Reihenfolge zu bringen. Dies erfolgt unter Berücksichtigung des Versandtermins und der maximal zulässigen Kapazität bei dem nachfolgenden Bearbeitungsschritt.
Schon beim Anstoßen der Werkstücke findet all dies bereits Anwendung, um mit dem Gesamtsystem möglichst wirtschaftlich arbeiten zu können.
Sortierspeicher
Wir entwickeln für Sie die Lösung der Zukunft
Lassen Sie uns Ihre individuellen Anforderungen zukommen.
Wir arbeiten Ihnen ein auf Sie zugeschnittenes Konzept aus.
Wir arbeiten Ihnen ein auf Sie zugeschnittenes Konzept aus.
Das System
Direkter Zugriff auf Einzelteile
Mechanisch sind die Systeme aufgebaut wie ein stehendes Regalbediengerät, welches links und rechts mit einem Kragarmregal komplettiert ist. Auf die Kragarme werden Einzelteile abgelegt, so dass der Etagensprung der einzelnen Kragarme entsprechend der Plattendicken recht eng ausgelegt werden kann. Unterschiedliche Etagensprünge für die unterschiedlichen Plattendicken sind innerhalb des Speichers möglich. Der eigentliche Vorteil des Systems liegt im direkten Zugriff auf jedes einzelne Teil in jeder Sektion der Etage.Einteilung in Sektionen
Der Kompaktsortierspeicher ist in der Länge in mehrere gleich lange Sektionen unterteilt. Die Länge der Sektionen ist abhängig von der durchschnittlichen Teilelänge. Das Teleskopsystem des Bediengerätes wird in identische Sektionen unterteilt. Die einzelnen Sektionen können einzeln oder kombiniert bedient werden.Mehrfachtiefe Lagerung
Damit auch die Kragarmtiefe immer optimal genutzt werden kann, befindet sich zwischen den Teleskopen der Hubplattform eine Verschiebeeinrichtung, die kleine Teile während des Hubes horizontal so platzieren kann, dass andere Teile in der gleichen Ebene ebenfalls noch davor abgelegt werden können. Die große Packungsdichte der Systeme wird durch das Kombinieren der Sektionen erreicht. In einer Vielzahl von Sektionen wird mehrfachtief gelagert, und dies je Etage zu beiden Seiten des Bediengerätes.
Beispiel eines Kompaktsortierspeicherblocks
Ausgehend von den in der Möbelindustrie durchschnittlichen Abmessungen der Teile von ca. 1.000 x 500 mm bedeutet dies, dass bei einer Kragarmtiefe von ca. 1.300 mm sowie 6 Sektionen in der entsprechenden Länge und ca. 55 Etagen links und rechts des Bediengerätes (entspricht einer Hallenhöhe von ca. 6 m) eine Kapazität von max. 1.320 Teilen innerhalb eines Sortierspeichers zur Verfügung steht.
Es ist problemlos möglich, weitere Sortierspeicher in Reihe hintereinander zu schalten, um die Kapazität bzw. die Sortierleistung entsprechend der erforderlichen Auslastung der angebundenen Maschinen bzw. der erforderlichen Pufferkapazität auszulegen.Hohe mechanische Taktleistung der Sortiersystems
Die mechanische Taktleistung eines Speichers liegt bei ca. 3 Takten pro Minute. Bei angenommenen 6 separaten Sektionen auf dem Bediengerät bedeutet dies, dass im besten Fall 3 mal 6 Teile pro Minute transportiert werden können.
Die zu lagernden Mengen innerhalb eines Speichers und die notwendigen Zykluszeiten müssen in Abhängig von Teilegrößen, Einbauabmessungen und Gewichten bei der Auslegung des Systems berücksichtig werden.
Anhand der ermittelten Daten kann entschieden werden, ob ein, zwei oder mehr Speicher erforderlich sind. Es ist möglich, mehrere Ein- und Ausgänge innerhalb eines Speichers zu verwalten.
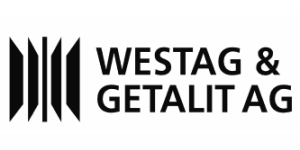
Sortierspeicher Westag

Sortierspeicher Horatec